A Comprehensive Guide to Calibrating Pressure Switches with a Focus on Dead Band Optimization
Abstract:
Pressure switches play a critical role in various industrial applications, ensuring the safety and efficiency of processes by monitoring and controlling pressure levels. Calibrating these devices is essential to maintain accuracy and reliability. This white paper delves into the intricacies of calibrating pressure switches, emphasizing the significance of dead band optimization for enhanced performance.
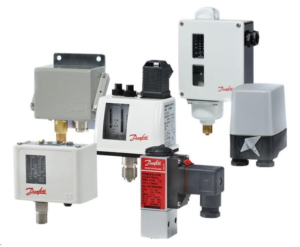
Introduction:
Pressure switches are fundamental components in industrial settings, controlling and monitoring pressure to safeguard equipment and processes. Calibrating these switches is crucial to ensure accurate and reliable operation. This white paper aims to provide a comprehensive guide to the calibration process, with a particular focus on optimizing the dead band.
Understanding Pressure Switch Calibration:
Calibration is the process of adjusting a device to ensure its measurements align with a standard reference. For pressure switches, this involves configuring the switch to respond accurately to variations in pressure levels. Proper calibration guarantees that the switch provides precise readings, preventing equipment damage and ensuring operational safety.
Key Components of a Pressure Switch:
Before delving into calibration, it’s essential to understand the key components of a pressure switch. These typically include a pressure-sensing element, set-point adjustment, electrical contacts, and hysteresis or dead band adjustment.
• Pressure-sensing element: This is the part of the switch that responds to changes in pressure. It could be a diaphragm, bellows, or other technologies depending on the application.
• Set-point adjustment: The set-point is the pressure level at which the switch activates or deactivates. Adjusting the set-point is a crucial part of calibration.
• Electrical contacts: These contacts open or close based on the pressure changes, triggering electrical signals to control the connected system.
• Hysteresis or dead band: The dead band is a range of pressures within which the switch remains inactive, preventing rapid and unnecessary switching in applications with fluctuating pressures.
The Importance of Dead Band Optimization:
Dead band, also known as hysteresis, is a critical factor in pressure switch calibration. It represents the pressure range where the switch remains inactive after deactivation or before activation. Optimizing the dead band is essential for several reasons:
• Preventing Rapid Switching: A well-optimized dead band prevents the pressure switch from rapidly switching on and off in response to minor pressure fluctuations. This reduces wear and tear on the switch and connected equipment.
• Enhancing Stability: Dead band optimization contributes to the stability of the controlled system. It minimizes unnecessary interruptions, ensuring smoother operation.
• Avoiding False Alarms: A narrow dead band helps avoid false alarms triggered by minor pressure variations, enhancing the reliability of the pressure switch.
• Increasing Lifespan: By minimizing unnecessary switching, dead band optimization contributes to extending the lifespan of the pressure switch and
connected components.
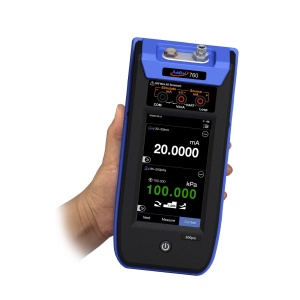
Steps in Pressure Switch Calibration:
Calibrating a pressure switch involves several steps, each crucial for achieving accurate and reliable performance. The process can vary based on the type of pressure switch and the specific application, but the following general steps provide a foundation for calibration:
1. Identify Calibration Requirements: Understand the application’s pressure requirements and determine the desired set-point and dead band values.
2. Prepare the Calibration Equipment: Use calibrated pressure sources, gauges, and a multimeter to ensure accurate measurements during the calibration process. Additel’s model 760 in place of a traditional multimeter is a great tool for helping to automate much of this process.
3. Connect the Pressure Source: Connect the pressure source to the pressure switch, ensuring a secure and leak-free connection.
4. Adjust Set-Point: Gradually increase the pressure to the desired set-point while monitoring the switch’s activation. Adjust the set-point until it aligns with the specified pressure level.
5. Calibrate Dead Band: Fine-tune the dead band to optimize the pressure switch’s performance. This involves adjusting the range within which the switch remains inactive.
6. Verify Calibration: Confirm the calibration by comparing the pressure switch’s readings with the calibrated pressure source. Make any necessary adjustments to achieve accuracy.
7. Document Calibration Data: Record the calibration settings and results for future reference. This documentation is crucial for traceability and quality control.
8. Perform Periodic Calibration: Regularly calibrate pressure switches to account for wear and environmental changes, ensuring continued accuracy and reliability.
Challenges in Pressure Switch Calibration:
Despite the importance of calibration, several challenges can arise during the process:
• Environmental Factors: Changes in temperature, humidity, and atmospheric pressure can affect calibration accuracy.
• Wear and Tear: Continuous use can lead to wear and tear of the pressure switch components, necessitating frequent calibration.
• Mechanical Drift: Over time, mechanical components may experience drift, impacting the switch’s set-point and dead band.
• Fluid Compatibility: In applications involving corrosive or abrasive fluids, the pressure switch’s components may degrade, affecting calibration.
Advanced Calibration Techniques:
To overcome challenges and enhance calibration precision, advanced techniques and technologies are being employed in modern industrial settings:
• Digital Calibration: Digital pressure switches offer precise calibration through digital interfaces, allowing for more accurate adjustments.
• Remote Calibration: Some pressure switches support remote calibration, enabling adjustments without physical access to the switch. This is particularly useful in inaccessible or hazardous environments.
• Automated Calibration Systems: Integration with automated calibration systems streamlines the calibration process, reducing human error and increasing efficiency.
• Condition Monitoring: Implementing condition monitoring systems allows for real-time tracking of pressure switch performance, enabling proactive calibration and maintenance.
Case Studies:
To illustrate the practical application of pressure switch calibration and dead band optimization, consider the following case studies:
• Manufacturing Industry: In a manufacturing plant using pressure switches to control hydraulic systems, optimizing dead band prevented unnecessary system shutdowns, improving overall efficiency.
• Oil and Gas Sector: In oil and gas applications, precise pressure control is critical. Dead band optimization in pressure switches contributed to better stability and reduced false alarms in offshore drilling operations.
• Chemical Processing Plant: A chemical plant utilizing pressure switches for monitoring corrosive fluids benefited from advanced digital calibration, ensuring accurate measurements and prolonged switch lifespan.
Future Trends in Pressure Switch Calibration:
As technology continues to advance, the field of pressure switch calibration is expected to see several trends:
• IoT Integration: Internet of Things (IoT) integration allows for real-time monitoring and calibration adjustments, enhancing overall system reliability.
• Machine Learning Algorithms: Implementing machine learning algorithms can predict and compensate for calibration drift, reducing the frequency of manual calibrations.
• Wireless Connectivity: Wireless communication capabilities enable remote calibration and data retrieval, making the process more convenient and efficient.
• Smart Sensors: The development of smart pressure sensors with built-in calibration capabilities will revolutionize the calibration landscape, simplifying maintenance tasks.
Conclusion:
Calibrating pressure switches is a critical aspect of ensuring the accuracy, reliability, and safety of industrial processes. Dead band optimization plays a pivotal role in enhancing the performance of pressure switches, contributing to stability and longevity. As technology advances, the integration of digital interfaces, automation, and smart sensors will further streamline the calibration process, paving the way for more efficient and sophisticated industrial systems.
Check out our NATA accredited calibration services that we perform here in our facilty: https://www.zedflo.com.au/our-services/calibration-services-overview/